Unlocking the Secrets of Four Pole Solenoid Testing
Ever felt the subtle hum of a hidden force, the quiet click of an unseen mechanism? That, my friend, could be the magic of a four pole solenoid at work. These unassuming electromechanical marvels are the unsung heroes of countless devices, from washing machines to sophisticated industrial equipment. But what happens when this silent workhorse falters? How do you diagnose the issue? This exploration delves into the art of four pole solenoid testing, empowering you to unravel the mysteries of these powerful components.
Understanding how to assess the health of a four pole solenoid is crucial for maintaining the smooth operation of any system relying on these devices. Whether you're a seasoned technician or a curious DIY enthusiast, mastering the techniques of solenoid testing can save you time, money, and frustration. This journey will illuminate the path to effective solenoid diagnostics.
The history of solenoid testing is intertwined with the evolution of electromagnetic technology. From early experiments with magnetism to the sophisticated diagnostic tools of today, the quest to understand and control these forces has driven innovation. As solenoids became more integral to modern machinery, the need for reliable testing methods grew in parallel, leading to the development of specialized procedures and equipment.
The core principle of solenoid testing involves verifying the electromagnetic field generated when energized. A four pole solenoid, unlike its simpler two-pole counterpart, offers enhanced control and efficiency due to its more complex magnetic field. This intricacy necessitates a nuanced approach to testing, ensuring that all poles are functioning as intended. Common issues include open coils, short circuits, and mechanical sticking, all of which can be diagnosed through appropriate testing methods.
A four-pole solenoid is essentially an electromagnet with four distinct magnetic poles. When energized, these poles create a magnetic field that actuates a plunger or armature. Testing a four pole solenoid involves verifying that each pole generates the expected magnetic field and that the mechanical action is smooth and consistent. A simple example involves applying a controlled voltage and observing the plunger movement. If the movement is sluggish, jerky, or absent, further investigation is warranted.
Testing your solenoid provides several key benefits. Firstly, it allows for preventative maintenance, identifying potential issues before they escalate into costly failures. Secondly, accurate diagnosis streamlines troubleshooting, reducing downtime and repair expenses. Finally, regular testing ensures optimal solenoid performance, maximizing the efficiency and longevity of the equipment it powers. For example, testing a washing machine solenoid before it completely fails can prevent a flooded laundry room and a hefty repair bill.
An effective solenoid testing strategy involves a step-by-step approach. Begin by visually inspecting the solenoid for any obvious damage. Next, use a multimeter to check for continuity in the coil windings. Finally, apply a controlled voltage and observe the plunger movement. A successful test will reveal smooth, consistent actuation. Documenting your findings throughout the process helps track performance over time.
Here's a checklist for testing a four pole solenoid:
1. Visual inspection for damage.
2. Continuity test with a multimeter.
3. Controlled voltage application and plunger observation.A step-by-step guide:
1. Disconnect the solenoid from the circuit.
2. Visually inspect for cracks, burns, or loose connections.
3. Set your multimeter to ohms and test for continuity across the coil terminals.
4. Reconnect the solenoid and apply the rated voltage.
5. Observe the plunger movement for smooth, consistent actuation.Advantages and Disadvantages of Testing a Four Pole Solenoid
Advantages | Disadvantages |
---|---|
Preventative maintenance | Requires specialized tools in some cases |
Streamlined troubleshooting | Can be time-consuming for complex systems |
Optimized solenoid performance | Potential for misdiagnosis if not performed correctly |
Five best practices: 1. Always disconnect the solenoid before testing. 2. Use the correct voltage rating. 3. Observe proper safety precautions. 4. Document your findings. 5. Consult the manufacturer's specifications.
Real-world examples: 1. Testing a car starter solenoid. 2. Checking a washing machine water inlet solenoid. 3. Testing a hydraulic valve solenoid. 4. Evaluating an industrial automation solenoid. 5. Testing a vending machine dispensing solenoid.
Challenges and solutions: 1. Intermittent failures: Use an oscilloscope to capture transient signals. 2. Difficult access: Employ specialized test probes. 3. Complex circuitry: Consult wiring diagrams. 4. Damaged connectors: Replace faulty connectors. 5. Burned coils: Replace the solenoid.
FAQ: 1. What is a four pole solenoid? 2. How does a four pole solenoid work? 3. What are common solenoid failures? 4. How can I test a solenoid? 5. What tools do I need? 6. What precautions should I take? 7. How often should I test solenoids? 8. Where can I find more information?
Tips and Tricks: Using a magnetic field sensor can help visualize the magnetic field strength and distribution of each pole. This can be particularly useful for identifying weak or uneven magnetic fields that might not be apparent through simple plunger observation. Additionally, consulting online forums and communities dedicated to electronics and mechanics can provide valuable insights and troubleshooting tips.
In conclusion, mastering the art of four pole solenoid testing is an invaluable skill for anyone working with electromechanical systems. By understanding the principles of solenoid operation, implementing effective testing procedures, and staying informed about best practices, you can ensure optimal performance, prevent costly failures, and extend the lifespan of your equipment. This knowledge empowers you to confidently diagnose and troubleshoot solenoid issues, enhancing your ability to maintain and repair a wide range of devices. So, embrace the power of knowledge, delve into the world of solenoid diagnostics, and unlock the secrets of these electromechanical marvels. By proactively addressing potential issues, you not only save time and resources but also contribute to a more sustainable and efficient approach to technology. Start testing your solenoids today and experience the peace of mind that comes with knowing your equipment is in top working condition.
Decoding apa format font size and style guidelines
Goodnight sweet dreams god bless a deeper look at a beloved phrase
Unlocking literacy the power of short readings for first graders


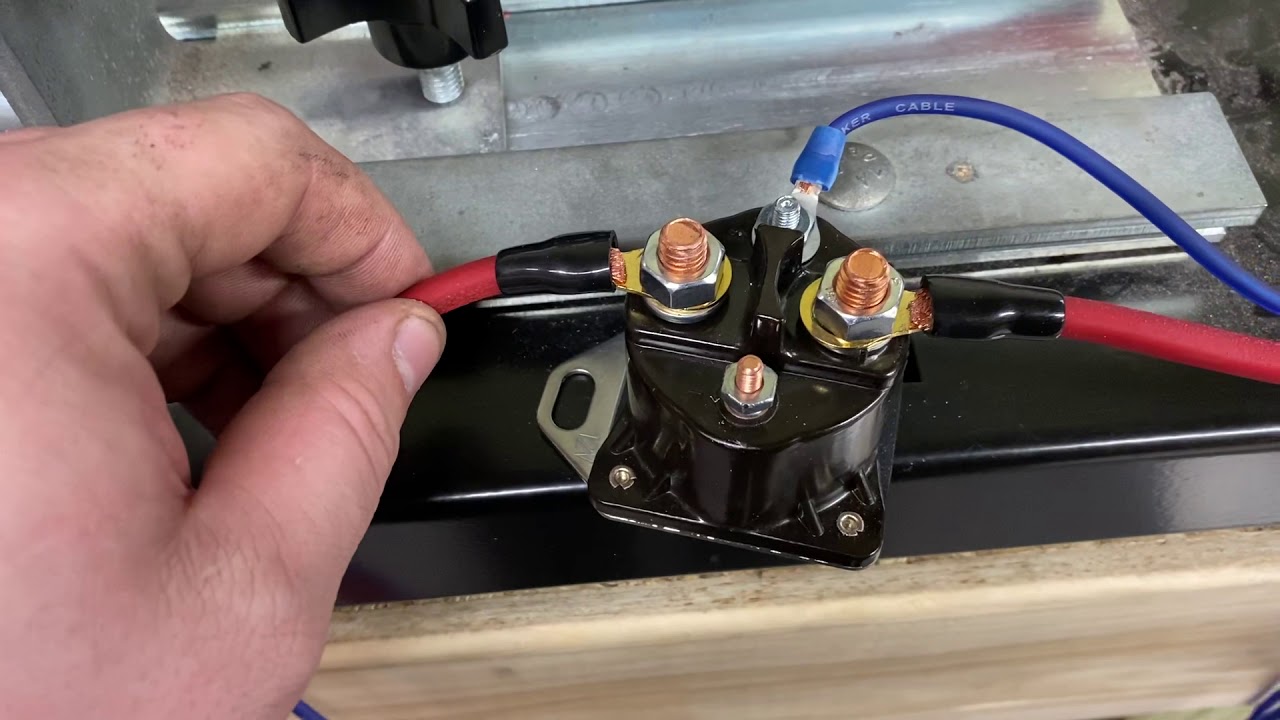










