The Silent Storyteller: Deciphering Your Fuel Gauge Sender
There’s a certain elegance in the simplicity of a fuel gauge, a subtle curve whispering promises of journeys yet to come. But behind that unassuming dial lies a story, a mechanism quietly working to translate the language of liquid fuel into a visual narrative. This is the story of the fuel gauge sender unit, the unsung hero of every road trip, the silent storyteller of your vehicle's fuel reserves.
The fuel level indicator, often taken for granted, is a critical component ensuring drivers aren't stranded with an empty tank. It's a small but mighty device, translating the raw data of fuel volume into a digestible metric we all rely on. Think of it as the interpreter between your fuel tank and your dashboard, constantly communicating the vital information needed to keep you moving.
From vintage automobiles to modern electric vehicles with range indicators, the basic principle remains the same: accurately measuring the amount of fuel available. This task falls to the fuel gauge sending unit, often located within the fuel tank itself. This unit, with its float and variable resistor, acts as the eyes of the fuel system, constantly monitoring the liquid level and relaying this information to the gauge.
The history of the fuel gauge sending unit mirrors the evolution of the automobile. Early systems were rudimentary, sometimes relying on simple float mechanisms connected to levers. As technology advanced, so did the sophistication of these units, incorporating electrical resistance and, more recently, digital sensors for greater precision. The development of more accurate and reliable fuel sending units has played a crucial role in enhancing the driving experience and mitigating the anxiety of running out of fuel.
Common problems associated with fuel sender units can include inaccurate readings, sticking floats, and electrical malfunctions. These issues can stem from a variety of factors, such as corrosion, wear and tear, or damage to the wiring. Troubleshooting these problems often involves inspecting the unit for physical damage, testing the electrical connections, and potentially replacing the entire unit.
The fuel level sensor, a key component of the sending unit, typically uses a float connected to a variable resistor. As the fuel level changes, the float moves, altering the resistance. This change in resistance is then interpreted by the fuel gauge, providing a visual representation of the fuel level. A common issue is a faulty float, which can lead to inaccurate or erratic readings.
Benefits of a properly functioning fuel sender unit are numerous: accurate fuel level readings, preventing unexpected fuel outages, and allowing for better trip planning. Imagine embarking on a long journey only to discover your fuel gauge is unreliable. The peace of mind offered by a functioning fuel level sensor is invaluable.
Maintaining a well-functioning fuel system is paramount. Regular checks of the fuel gauge system, including the sending unit, are crucial. This might involve visually inspecting the wiring and connections, or having a mechanic perform a more thorough diagnostic test. Addressing potential issues early can prevent more significant problems down the line.
Advantages and Disadvantages of Fuel Gauge Sender Units
Advantages | Disadvantages |
---|---|
Provides accurate fuel level information | Subject to wear and tear |
Enables better trip planning | Can be affected by corrosion |
Prevents running out of fuel unexpectedly | Can malfunction, leading to inaccurate readings |
Best practices for maintaining your fuel system and ensuring the longevity of the fuel gauge sending unit include regular inspections, avoiding running the tank consistently low (which can expose the sending unit to more debris), and using quality fuel. Addressing any fuel system issues promptly can prevent small problems from escalating into costly repairs.
Frequently Asked Questions:
1. How does a fuel gauge sender work? It uses a float attached to a variable resistor. As the fuel level changes, the float moves, changing the resistance and sending a signal to the gauge.
2. What are common problems with fuel senders? Sticking floats, faulty resistors, and wiring issues.
3. How do I test a fuel sender? Often involves testing the resistance with a multimeter.
4. Can I replace a fuel sender myself? Often a DIY project, but may require specialized tools.
5. How much does a fuel sender unit cost? Varies depending on the vehicle make and model.
6. How often should I check my fuel sender? Regular checks as part of routine vehicle maintenance are recommended.
7. What are the symptoms of a bad fuel sender? Inaccurate or erratic fuel gauge readings.
8. Can a bad fuel sender damage my car? While not directly damaging, it can lead to running out of fuel, which can cause other issues.
The fuel gauge sender unit, while often overlooked, is a vital component of any vehicle. It's the silent partner ensuring we reach our destinations, providing the crucial information that keeps us moving. From the earliest float mechanisms to modern digital sensors, the evolution of the fuel level sending unit has mirrored the progress of the automobile itself. Understanding its function, potential problems, and maintenance is essential for every driver. By appreciating this small but significant component, we can ensure smoother, more confident journeys, knowing that the silent storyteller of our fuel tank is always at work.
Unlocking the world of multichannel sports a comprehensive guide
Kansas city chiefs tattoo inspiration a fans guide to ink
The enduring appeal of a pre owned toyota rav4 hybrid




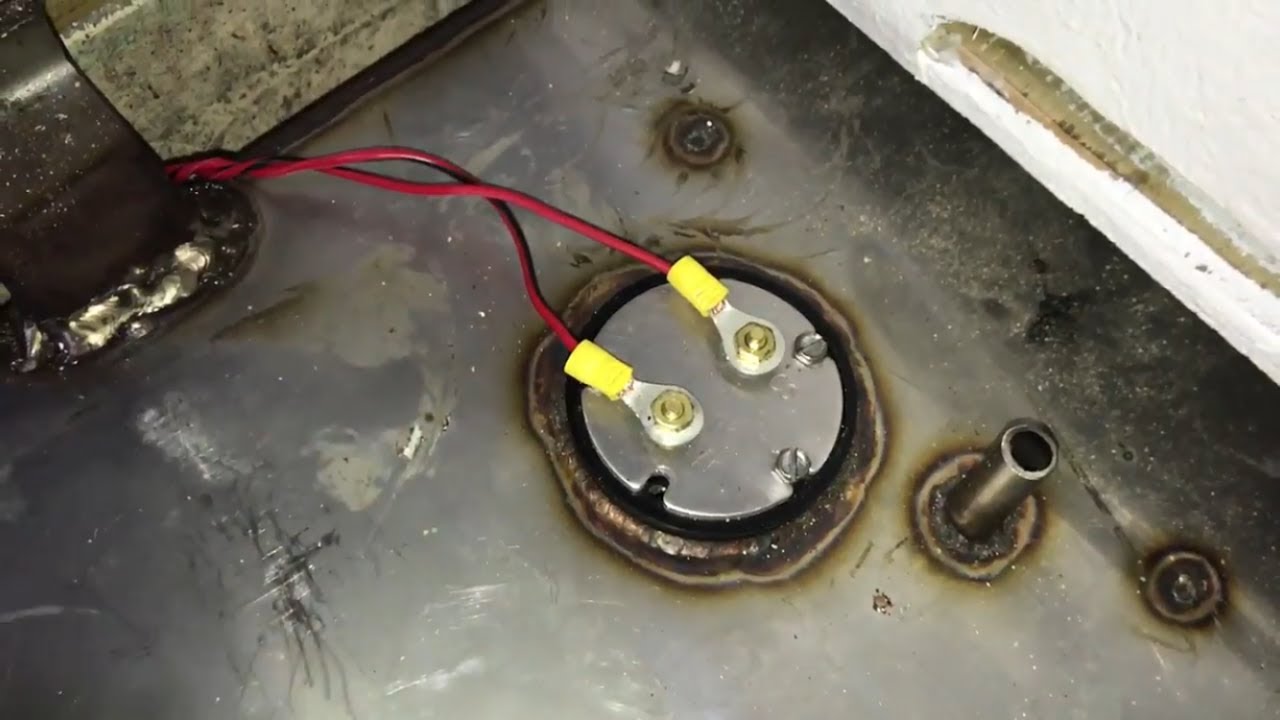








